Data & Process Mining
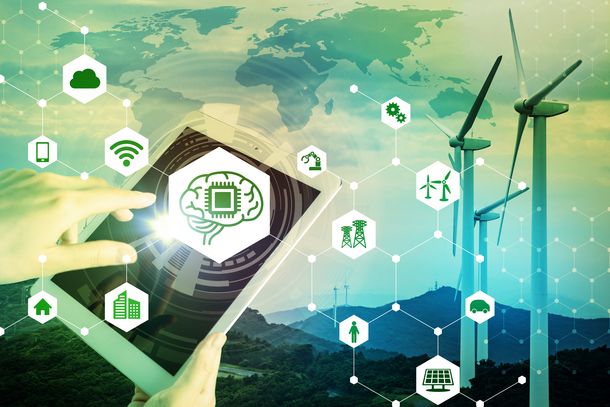
Companies and organizations in many industrial and service sectors have done their homework in recent years when it comes to digitalization. The steadily increasing digital monitoring and partial automation of processes, the equipping of equipment with sensors and actuators, and ever more comprehensive system integrations have led to the existence of large quantities of process and machine data - both on the part of the machine manufacturer and the user. Both on the part of the machine manufacturer and on the part of the user. Machine manufacturers in particular have seen this development as an opportunity to expand their competitive positions by offering additional digital services. The primary objectives here are to optimize process control on the user side and, at the same time, to leverage savings potential through condition-based maintenance strategies by means of condition monitoring. In addition, the evaluation of the (field) data obtained also holds enormous potential for the company's own organization. The R&D departments gain a much better understanding of the exact operating conditions and usage behavior of the machines - valid data series instead of multi-moment recordings paired with proprietary empirical knowledge of employees. Performance characteristics and functionalities of machines can be adapted and optimized in a much more targeted manner on this basis and enable the stocking and maintenance strategy to be designed specifically for the customer or the machine. Industry has understood that the sustainable strengthening of its own competitive position - both in production and among equipment manufacturers - lies in the area of data analysis - beyond its own system boundaries with interfaces into the peripheral systems. However, the actual spectrum of requirements is still very diffuse today: For some, the mere visualization of sensor data with a focus on the reliability and validity of the data is sufficient, while others see this as the key to achieving process stability and reproducibility independent of the actual knowledge of the cause-and-effect relationships in complex systems. The common goal is to go beyond the heuristic approaches of the lean paradigms to evidence-based process improvements based on data analysis and statistical and self-learning models.
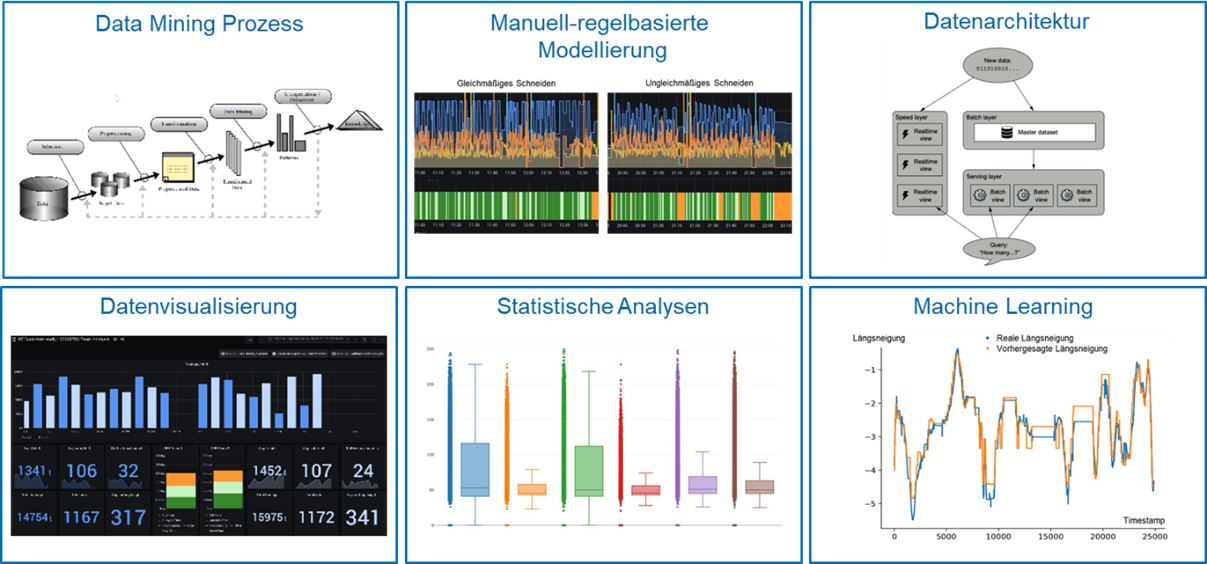